Mosolver Technology Enables Harsh Environment Operation
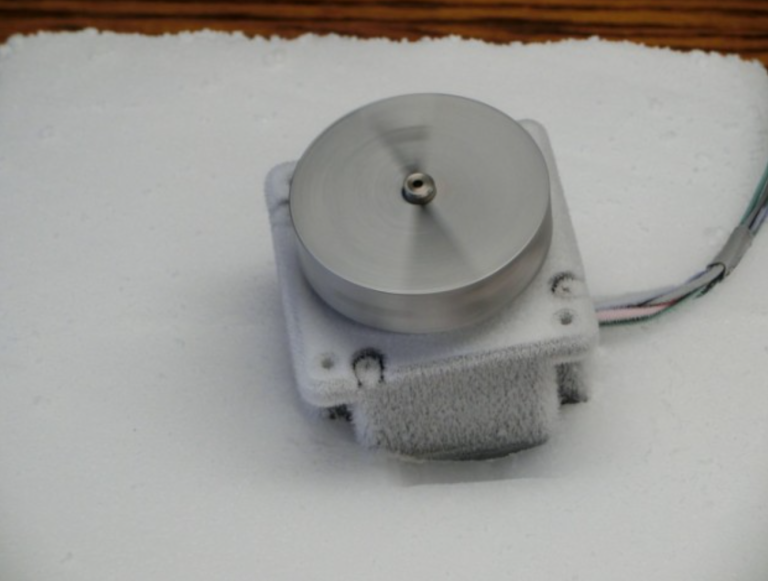
Interesting Projects Blog
April 23 2024 | Donald P. Labriola PE
The MosolverTM – a combined Motor and Resolver – uses the existing motor magnetic structure and drive elements, in combination with a unique sensor within the motor to deliver 32,000 positions per revolution as well as commutation information even when the motor is stationary. As the sensor is based on a rugged polyimide sensor coil, the environmental limits of the servo actuator are primarily limited by the motor rather than the sensor system.
It is generally agreed that the feedback sensor is typically the weak-link in servo motor systems. In the case of encoder systems, the cleanliness of the disk and sensor, as well as the spacing between them are all critical to success. Grease displaced from a bearing or dust may disrupt the operation of the sensor. Resolvers with their feedback are more robust, but typically expensive. Both encoders and resolvers must be aligned to their motors for proper commutation phasing. The Mosolver grew out of a desire answer these robustness issues while also reducing the cost, size and weight of the system.
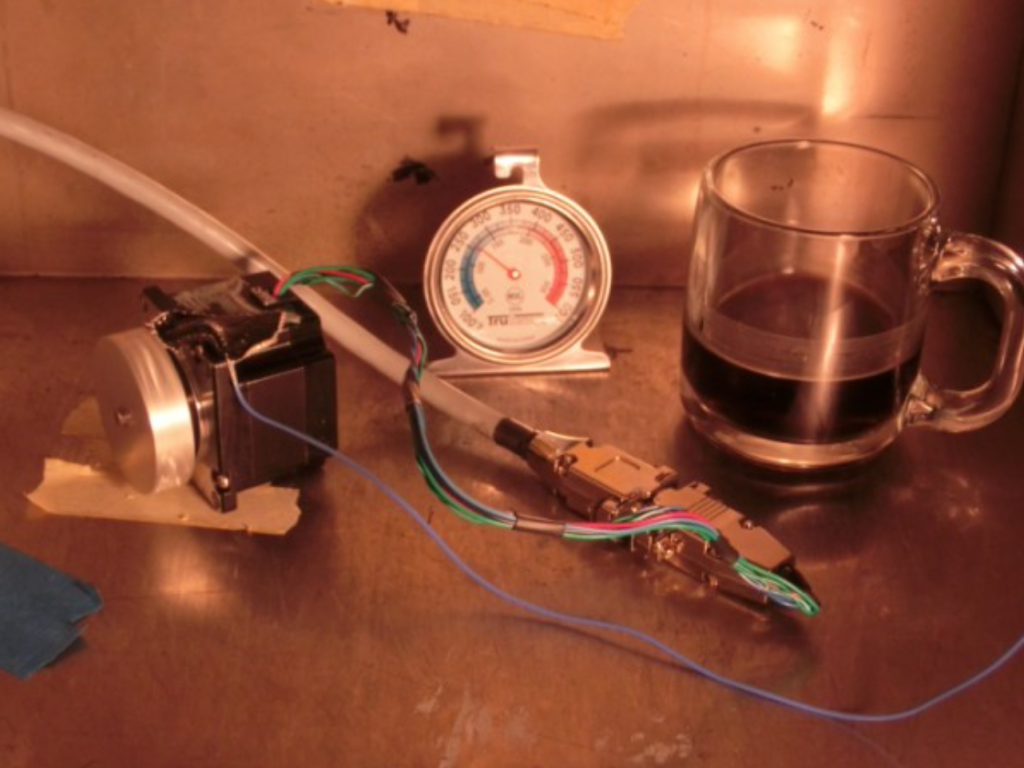
The sensor coils are built on a passive polyimide flex circuit, affixed within the motor stator structure in the process of motor assembly. The standard polyimide sensor material is rated from -80C to 180 C, with other formulations (substrate and adhesive systems) available with wide working temperature ranges from -269 C to 400 C. Polyimide flex circuits are also available in radiation resistant as well as low out-gassing formulations. When combined with a motor with similar ratings, the resulting Mosolver is capable of operating in a wide variety of harsh environments. With the sensor entirely encapsulated within the motor structure, the resulting Mosolver Hybrid Servo is the same size as the motor itself and does not require additional housings to protect the feedback element as would be required for a resolver or encoder, thus saving weight as well as space. As the sensor does not incorporate active devices nor moving elements, it has a high degree of robustness. The sensing method is AC based and is not subject to DC temperature drifts nor ambient magnetic fields as are hall effect devices. As the sensor is built into the same structure as the motor, no alignment/phasing adjustment is needed.
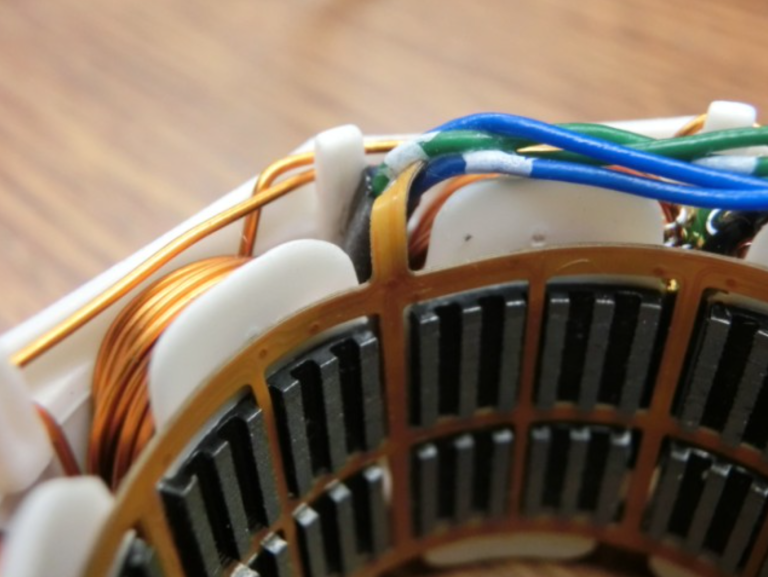
Physically, the Mosolver sense coils are embedded in between the stator teeth of the motor. These coils detect the flux variation caused by the stator ripple current normally associated with a PWM drive. The variation in current caused by the ripple current causes a flux variation, even when the motor is stationary. The flux, including the pulsing variation, is divided between different sections of the sense coil according to the tooth overlap between the rotor teeth and the stator teeth, the overlap varying with rotor position. When properly sampled in synchronism with the PWM drive, the sensor coil produces sine and cosine
information. The sine and cosine information is decoded into 640 positions for each of the 50 electrical cycles per revolution, resulting in 32000 positions per revolution. The sine and cosine information is also used for motor commutation without the need for a startup “wiggle” eliminating the startup transient. The Mosolver position feedback is maintained at zero speed, eliminating the drift associated with sensorless methods when maintaining position. Due to the construction, which shares the magnetic structure of the motor for both motion and sensing, the sensor is inherently aligned. Electronics to support the sensor consist of an amplifier for each of the two phases, and two A/D converters already present on the controlling DSP.
The technology may be applied to differing motor sizes, allowing for high resolution even in smaller motor frames where matching encoders are either expensive or are larger than the motor itself.
The technology is available in product format as well as being available for licensing for specialty motors.

Related Posts
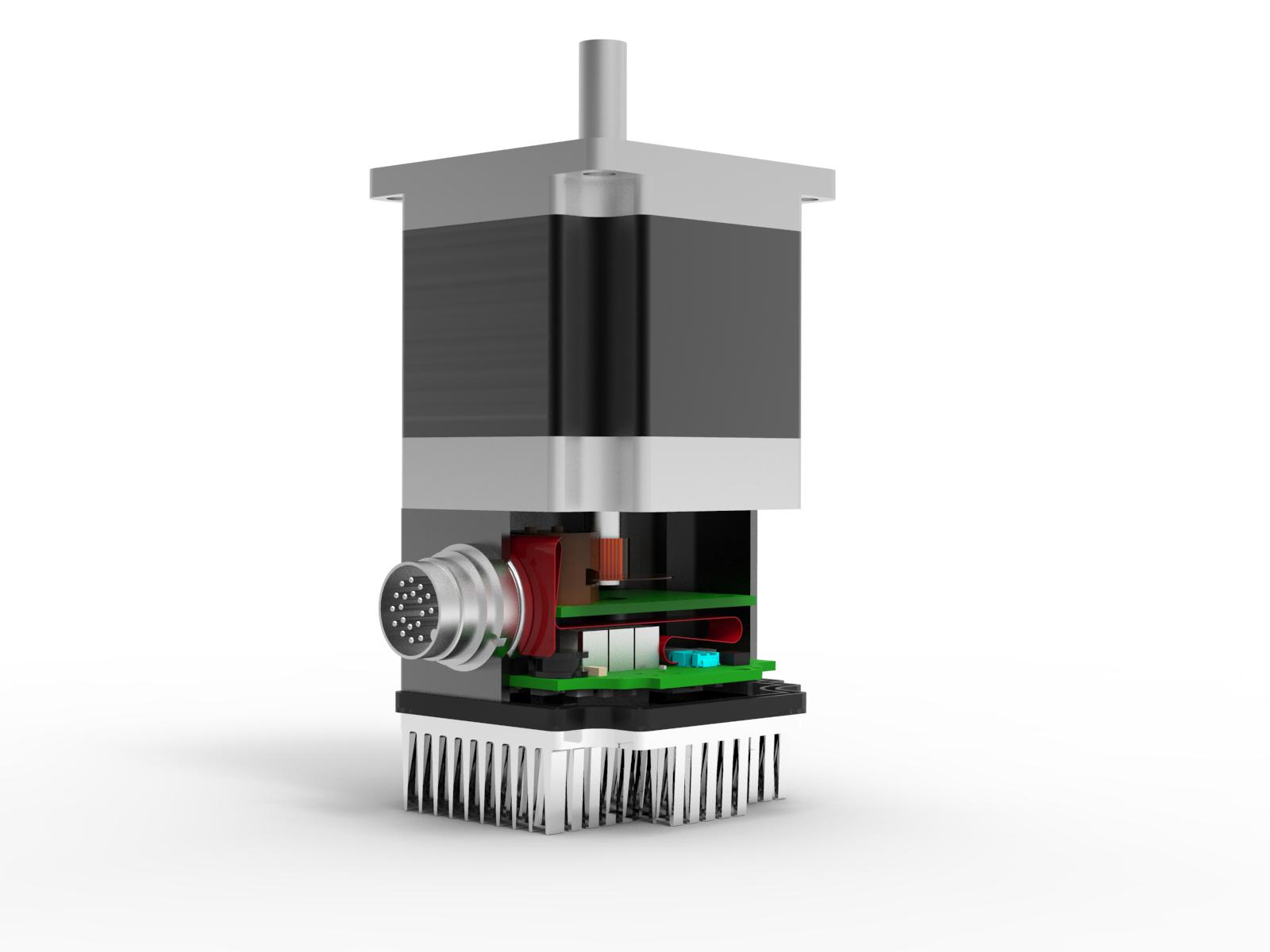
Operational Advantages of Integrated Motors
Operational Advantages of Integrated Motors Interesting Projects Blog April 17 2024 | Donald P. Labriola PE Combining a motor with
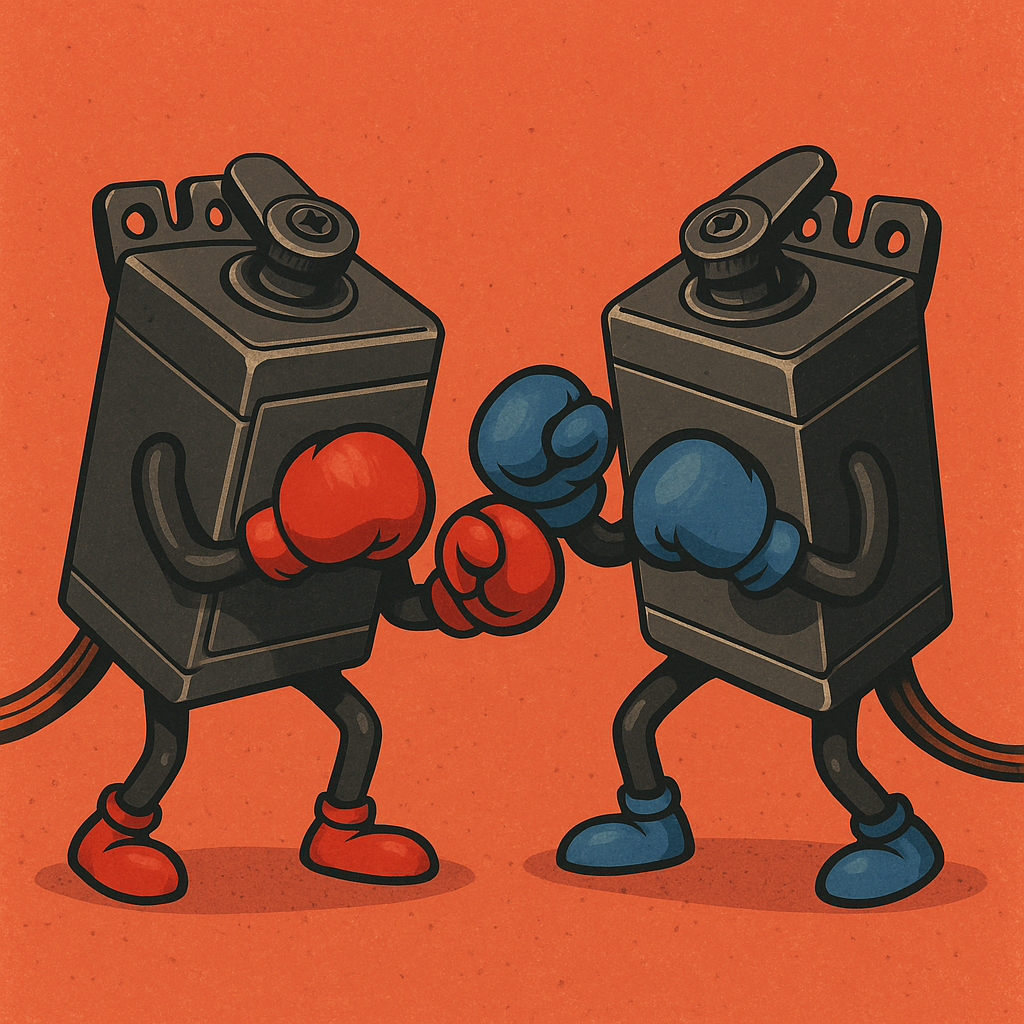
Integrated Hybrid Servo Motors Vs Standard Integrated Servo Motors
Integrated Hybrid Servo Motors Vs Standard Integrated Servo Motors Interesting Projects Blog April 10 2025 | Donald P. Labriola PE